雙系統(tǒng)的硬件架構(gòu)暗藏精密協(xié)同設計。制冷系統(tǒng)采用 “雙級壓縮 + 復疊式” 組合方案,低溫級選用 R23 制冷劑(沸點 - 82.1℃),高溫級匹配 R404A(沸點 - 46.5℃),通過板式換熱器實現(xiàn)能量梯級傳遞,單循環(huán)制冷量可達 12kW。制熱模塊則創(chuàng)新采用 “紅外輻射 + 電加熱絲” 雙源模式,24 組碳纖維紅外管(波長 2-5μm)實現(xiàn)面狀加熱,配合鎳鉻合金加熱絲的輔助補償,升溫速率達 25℃/min,較傳統(tǒng)單一加熱方式效率提升 70%。
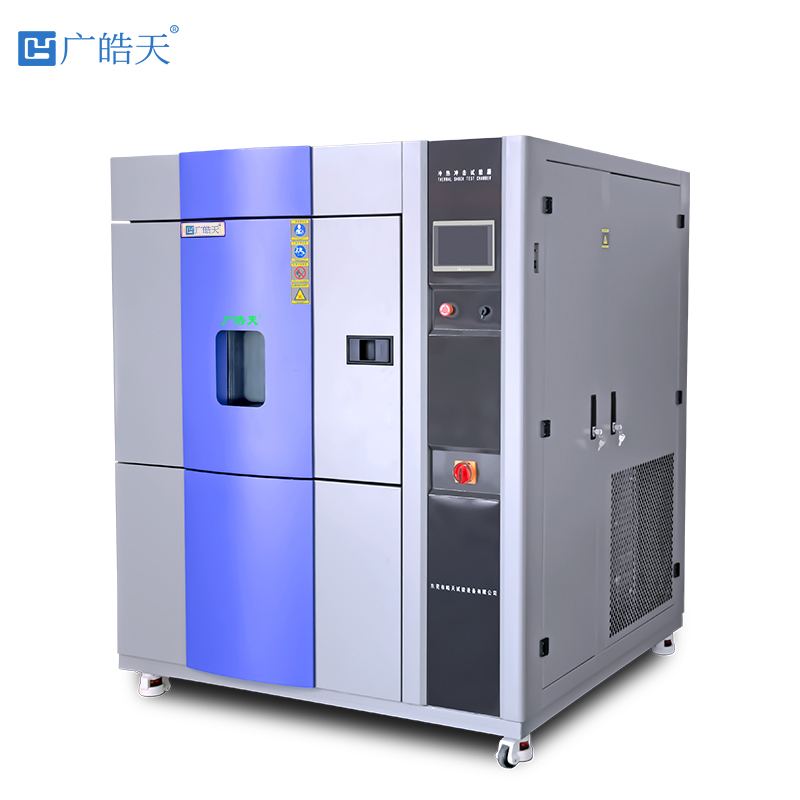
無縫切換的關鍵在于三重回路緩沖機制。當系統(tǒng)從 - 70℃切換至 150℃時,首先啟動預冷旁路,將高溫級制冷劑通過儲液罐暫存,避免冷熱介質(zhì)直接混合產(chǎn)生的壓力波動。同時,加熱模塊通過 PID 算法進行 3 秒預升溫,使紅外管表面溫度達到 500℃臨界值,縮短能量釋放延遲。位于風道系統(tǒng)的 6 組氣動風門則按 0.5 秒梯度切換,在阻斷制冷回路的同時逐步開啟制熱通道,實測顯示這一過程可使箱內(nèi)溫度波動控制在 ±0.8℃以內(nèi)。
智能控制算法是雙系統(tǒng)協(xié)同的 “神經(jīng)中樞”。基于 10 萬組歷史數(shù)據(jù)訓練的模糊神經(jīng)網(wǎng)絡,能實時預測溫度變化趨勢:當檢測到目標溫度切換指令時,系統(tǒng)會提前 0.3 秒調(diào)節(jié)膨脹閥開度(精度達 0.1mm),將制冷劑流量從 12kg/h 驟降至 3kg/h,同時將加熱功率從 0 線性提升至 15kW。某汽車零部件測試中,這套算法使 - 50℃至 120℃的切換過程耗時僅 8 秒,較傳統(tǒng) PLC 控制縮短 67%,且過沖量控制在 ±1.2℃。
能量回收系統(tǒng)的引入破解了冷熱對沖難題。在制冷轉(zhuǎn)制熱階段,板式換熱器將制冷回路的余熱(約 3.2kW)回收至熱水罐,通過循環(huán)泵輸送至加熱模塊預熱,使能源利用率提升 35%。而制熱轉(zhuǎn)制冷時,高溫空氣先經(jīng)熱管換熱器降溫 40℃,再進入蒸發(fā)器處理,避免制冷系統(tǒng)過載。半導體行業(yè)的實測數(shù)據(jù)顯示,該技術(shù)可使單次冷熱沖擊的能耗降低 28%,年節(jié)電達 1.2 萬度。


雙系統(tǒng)的可靠性依賴于冗余設計。制冷回路配備雙壓縮機(一用一備),當主壓縮機排氣壓力超 1.8MPa 時,備用機組在 0.5 秒內(nèi)自動投入運行。加熱模塊的每組分路均設置獨立溫控器,配合紅外測溫儀的實時監(jiān)測,可在 200ms 內(nèi)切斷故障單元。某航天產(chǎn)品測試的連續(xù)運行記錄顯示,這套冗余系統(tǒng)使設備切換次數(shù)突破 10 萬次,較單系統(tǒng)架構(gòu)提升 2.3 倍。
這種 “硬件互鎖 + 算法預判 + 能量循環(huán)” 的協(xié)同模式,不僅實現(xiàn)了溫度的極速切換,更保障了試驗數(shù)據(jù)的精準性。在新能源電池測試中,雙系統(tǒng)可在 - 40℃至 85℃區(qū)間內(nèi)完成 500 次循環(huán)沖擊,電芯容量衰減率的測試偏差控制在 0.5% 以內(nèi),為產(chǎn)品可靠性驗證提供了核心技術(shù)支撐。