定向跌落試驗機(jī)的核心競爭力,在于對 “角度" 和 “高度" 這兩個關(guān)鍵參數(shù)的把控。對于手機(jī)屏幕邊角抗摔測試、電池包棱邊沖擊驗證等場景,1° 的角度偏差或 1mm 的高度誤差,都可能導(dǎo)致測試數(shù)據(jù)失真,進(jìn)而誤導(dǎo)產(chǎn)品可靠性評估。那么,這類設(shè)備是通過哪些技術(shù)手段實現(xiàn)精準(zhǔn)控制的?本文將從機(jī)械結(jié)構(gòu)設(shè)計、驅(qū)動系統(tǒng)配置、智能控制算法三個層面,揭開定向跌落試驗機(jī)的 “精準(zhǔn)密碼"。
一、跌落角度控制:從 “機(jī)械限位" 到 “數(shù)字化校準(zhǔn)"
跌落角度的精準(zhǔn)性,直接決定了樣品沖擊位置的一致性。定向跌落試驗機(jī)通過 “多級調(diào)節(jié) + 剛性約束" 的組合方案,將角度控制誤差壓縮至 ±0.5° 以內(nèi),遠(yuǎn)低于普通跌落設(shè)備的 ±5° 水平。
1. 旋轉(zhuǎn)工作臺:角度調(diào)節(jié)的 “機(jī)械骨架"
設(shè)備的核心承載部件 —— 旋轉(zhuǎn)工作臺,是實現(xiàn)角度控制的基礎(chǔ)。其內(nèi)部采用精密渦輪蝸桿結(jié)構(gòu),配合滾珠絲杠傳動,可實現(xiàn) 0°-90° 范圍內(nèi)的無級調(diào)節(jié)。例如測試手機(jī)中框時,需將樣品傾斜 30° 以模擬 “邊角先落地" 的場景:操作人員通過手輪或伺服電機(jī)驅(qū)動工作臺旋轉(zhuǎn),角度刻度盤(最小精度 0.1°)實時顯示當(dāng)前角度,當(dāng)接近目標(biāo)值時,系統(tǒng)自動切換為微調(diào)模式(調(diào)節(jié)速度從 5°/s 降至 0.1°/s),避免過沖。
為防止角度漂移,工作臺還配備雙重鎖緊裝置:機(jī)械鎖緊銷(插入對應(yīng)角度定位孔)用于靜態(tài)固定,電磁制動器用于動態(tài)鎖止(響應(yīng)時間≤0.1s),確保樣品在跌落瞬間不會因慣性發(fā)生角度偏移。
2. 姿態(tài)定位工裝:適配復(fù)雜樣品的 “定制化方案"
對于異形樣品(如曲面屏手機(jī)、不規(guī)則電池包),僅靠工作臺旋轉(zhuǎn)難以保證精準(zhǔn)姿態(tài)。定向跌落試驗機(jī)通常配備模塊化定位工裝,通過以下方式實現(xiàn) “毫米級" 姿態(tài)控制:
3. 激光校準(zhǔn)系統(tǒng):動態(tài)修正角度誤差
即使機(jī)械結(jié)構(gòu)精度達(dá)標(biāo),長期使用后的部件磨損仍可能導(dǎo)致角度偏差。定向跌落試驗機(jī)內(nèi)置激光校準(zhǔn)模塊:測試前,激光發(fā)射器從 3 個不同方位發(fā)射激光束,照射樣品表面的定位靶標(biāo),系統(tǒng)通過分析激光反射點的位置偏差,自動計算當(dāng)前角度誤差,并驅(qū)動工作臺進(jìn)行補(bǔ)償(補(bǔ)償精度 0.01°)。例如某次測試中,系統(tǒng)檢測到實際角度比設(shè)定值小 0.3°,會立即控制渦輪蝸桿旋轉(zhuǎn)修正,整個過程在 10 秒內(nèi)完成,無需人工干預(yù)。

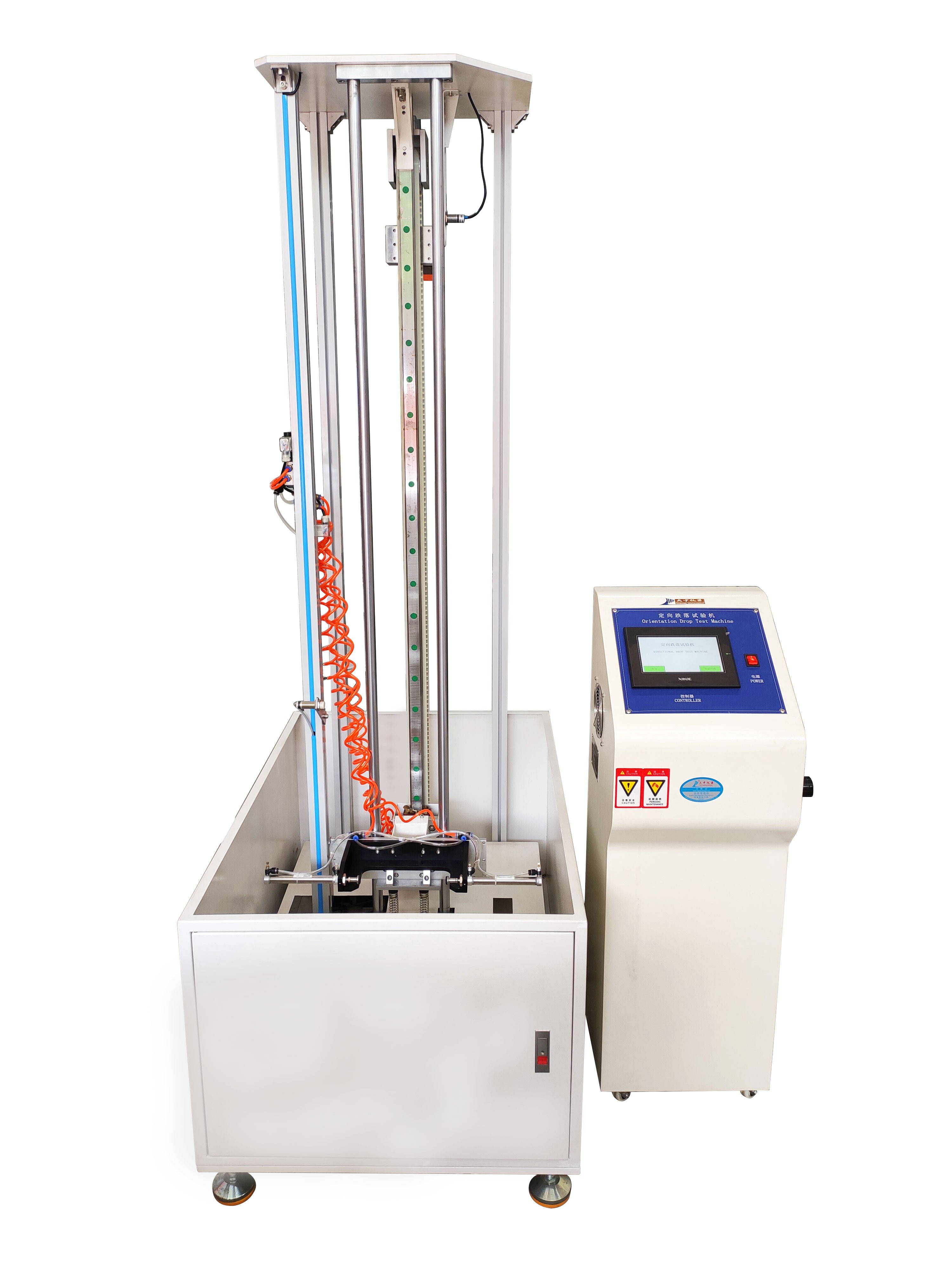
二、跌落高度控制:從 “機(jī)械標(biāo)尺" 到 “伺服閉環(huán)"
跌落高度直接決定沖擊能量(E=mgh)的大小,其控制精度需達(dá)到 ±1mm,才能確保沖擊能量的重復(fù)性(誤差≤1%)。定向跌落試驗機(jī)通過 “驅(qū)動系統(tǒng) + 測量反饋" 的閉環(huán)控制,實現(xiàn)從 0.1m 到 3m 的精準(zhǔn)高度調(diào)節(jié)。
1. 驅(qū)動系統(tǒng):三種主流方案的優(yōu)劣對比
不同驅(qū)動方式的設(shè)備,在高度控制精度和響應(yīng)速度上存在顯著差異:
無論哪種驅(qū)動方式,設(shè)備均配備機(jī)械限位裝置(如光電傳感器),當(dāng)升降臺接近最大高度時自動減速停止,避免機(jī)械碰撞。
2. 高度測量:從 “標(biāo)尺讀數(shù)" 到 “實時反饋"
傳統(tǒng)跌落臺依賴人工讀取標(biāo)尺高度,誤差常達(dá) 5mm 以上,而定向跌落試驗機(jī)通過多重測量手段確保精度:
這些測量數(shù)據(jù)實時傳輸至控制系統(tǒng),形成 “設(shè)定高度 - 實際高度 - 偏差修正" 的閉環(huán),確保每次跌落前的高度誤差≤1mm。
3. 釋放機(jī)構(gòu):“零延遲" 確保高度一致性
樣品釋放瞬間的 “滯后" 或 “提前",會導(dǎo)致實際跌落高度與設(shè)定值不符。定向跌落試驗機(jī)的釋放機(jī)構(gòu)采用以下設(shè)計消除誤差:
釋放機(jī)構(gòu)的動作由控制系統(tǒng)統(tǒng)一觸發(fā),確保樣品在升降臺到達(dá)預(yù)設(shè)高度后 “即刻釋放",避免因延遲導(dǎo)致的高度偏差。
三、控制系統(tǒng):智能化提升 “雙參數(shù)" 控制精度
機(jī)械結(jié)構(gòu)是精準(zhǔn)控制的基礎(chǔ),而智能控制系統(tǒng)則是 “大腦",通過算法優(yōu)化進(jìn)一步降低誤差,實現(xiàn)全流程自動化。
1. 人機(jī)交互界面:參數(shù)設(shè)置的 “可視化窗口"
操作人員可通過觸摸屏直接輸入目標(biāo)角度(如 30°)和高度(如 1m),系統(tǒng)自動計算對應(yīng)的機(jī)械位置參數(shù),并顯示實時角度、高度數(shù)值(刷新頻率 10Hz)。界面還支持存儲 100 組常用測試方案(如 “手機(jī)邊角跌落"“電池包棱邊沖擊"),下次使用時一鍵調(diào)用,避免重復(fù)設(shè)置。
2. 誤差補(bǔ)償算法:動態(tài)修正 “隱性偏差"
設(shè)備運(yùn)行中,溫度變化、樣品重心偏移等因素可能導(dǎo)致參數(shù)漂移,控制系統(tǒng)通過算法實時補(bǔ)償:
3. 數(shù)據(jù)追溯:測試過程的 “全程記錄"
每次測試的角度、高度數(shù)據(jù)(精確至 0.1° 和 0.1mm),以及對應(yīng)的時間、操作人員、樣品編號等信息,均自動存儲至本地數(shù)據(jù)庫,并支持導(dǎo)出 Excel 或 PDF 報告。這不僅滿足 ISO、ISTA 等標(biāo)準(zhǔn)對數(shù)據(jù)可追溯性的要求,也便于后期分析不同參數(shù)下的樣品損壞規(guī)律。
四、精度驗證:行業(yè)標(biāo)準(zhǔn)下的 “極限挑戰(zhàn)"
為確保設(shè)備精度達(dá)標(biāo),出廠前需通過嚴(yán)格的驗證測試: